Housing of Living in Limburg shows potential of circular roof renovation: cheaper, more efficient and more sustainable

In Lanaken, the roof of a social housing unit was renovated and additionally insulated, while the roof remained on the building! Wonen in Limburg, the Biesmans Group and V&B dakwerken joined forces for this unique pilot project. Innovation and creativity were combined with this brilliant result: an energetic and circular roof renovation at low cost, with minimal inconvenience for the residents.
Need for affordable housing
The pressure on the housing market is high. While the number of building permits for housing is at its lowest level in 22 years, the demand for energetic and affordable housing continues to grow. In Belgium, 75,000 housing units should be added each year until 2030 to meet housing demand.
Investing in sustainable renovation is therefore becoming increasingly important. This is all the more true for social housing. Because finding affordable housing solutions is a huge challenge, the waiting lists testify to that.
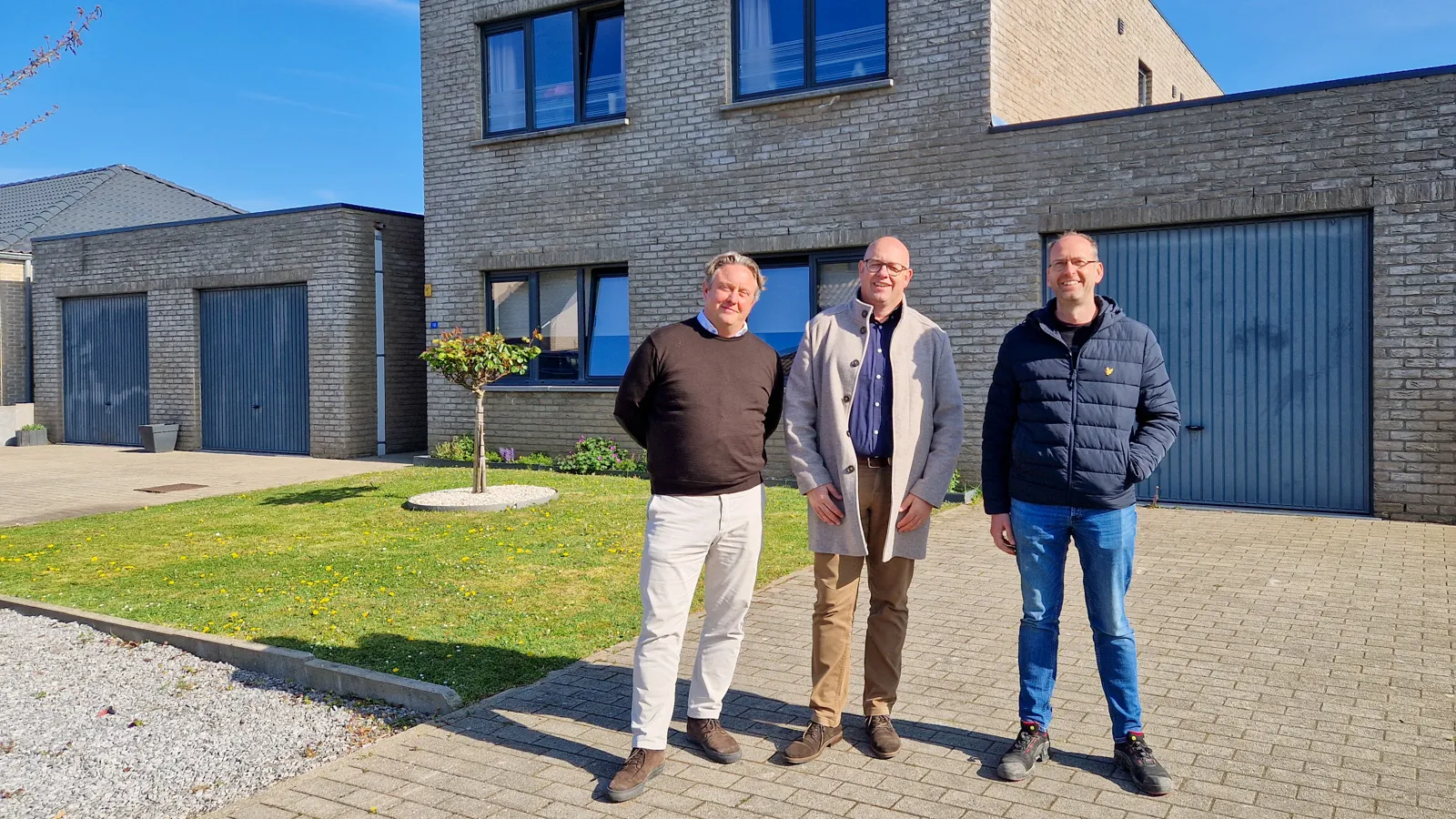
Leveraging existing materials for affordable housing
In that context, Wonen in Limburg (WiL) renovated a home in Lanaken, a unique unprecedented project. The existing EPDM roofing, which had been on the roof for almost 20 years, was reused. The ballast (gravel) was brought to one side of the roof, the EPDM was loosened and rolled up. This allowed additional insulation to be added. Then the EPDM was placed back and snapped into the bilge (up side of the roof) using the Certefix, a component of the BossCover Circular System. The ballast was put back in place. Then the other side of the roof area was addressed in a similar manner.
The Certefix is a system patented by Biesmans Group in which the EPDM membrane is clicked into the bilge, with no glue involved. This allows the roof to remain fully removable for the future.
The works were carried out by V&B Roofworks. Manager Gerry Briers is proud of the result: "The work progressed quickly because the ballast and the EPDM remained on the roof. The residents experienced minimal disruption."
Filip Biesmans, director of Biesmans Group, adds: "EPDM has a lifespan of at least 70 years, scientific research confirms. So you don't throw away a 20-year EPDM! Thanks to the BossCover Circular System, we can install the EPDM membrane loose-fit, and also reuse it in the future."
William Nelissen, WiL's technical innovation expert confirms, "The EPDM was still perfectly usable technically. By reusing it, we limited waste and reduced costs. And at the same time, we created a sustainable, circular roof. And that is exactly our mission".
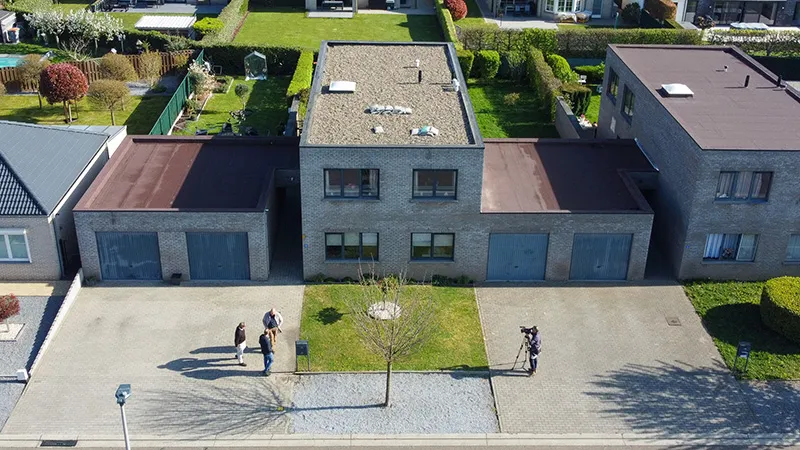
EPDM repurposed: more durable, lower cost, fast execution
The decision to reuse the existing EPDM roof waterproofing led to a successful trial run:
The circular roof structure proved significantly more economical than a complete renovation, accounting for an 18% savings.
In addition to the financial benefit, the implementation also proved to be practically more efficient. Thanks to the light weight of the additional insulation, it could be brought up by hand, eliminating the need for a mobile crane. Moreover, the existing EPDM layer and shingles did not have to be removed or transported from the roof. The residents were satisfied with the result: the site did not cause any nuisance in the garden and the lawn was not damaged.
One of the questions yet to be examined concerns the legal aspect of reuse. In principle, when renovating with new materials, a 10-year warranty period applies again. How do we address this when reusing materials that are already 20 years old? In this particular case (a 98 m² roof), the risk was considered manageable, thanks in part to the high level of confidence in the EPDM material. Moreover, several techniques exist today to test the waterproofing of a roof. On a larger scale, this remains a focus for the further application of circular principles in the construction industry.
This realization shows that circular construction is not only more sustainable, but also economically attractive and technically feasible. The project is thus a powerful example of how smart choices can make the construction sector more sustainable.
The project in Lanaken was a first test, but will certainly be followed up. In the meantime, Wonen in Limburg and Biesmans Group are looking at how this circular approach can be rolled out more widely.
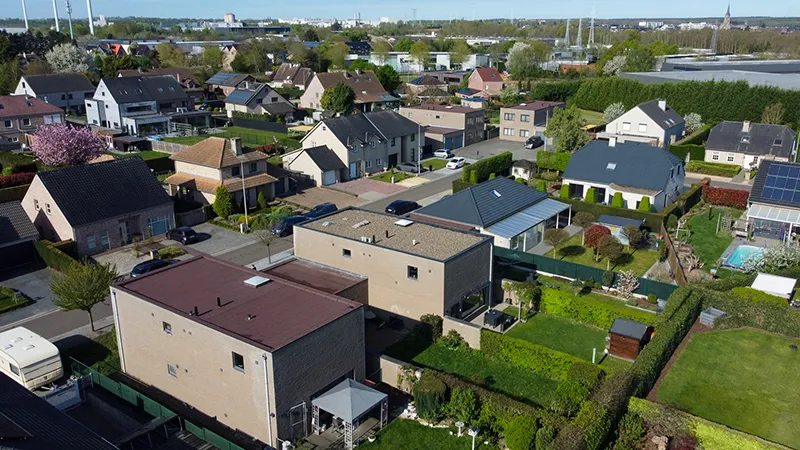
About Living in Limburg
Wonen in Limburg (WiL) is the housing company for those who want to rent, buy, rent or borrow socially in the province of Limburg. Within its mission "Together we create sustainable and affordable housing solutions everywhere in Limburg," WiL actively searches for sustainable and innovative renovation solutions. By working with partners such as Biesmans Group, Wonen in Limburg aims not only to improve the existing housing stock, but also to integrate circular principles into the social housing of tomorrow.
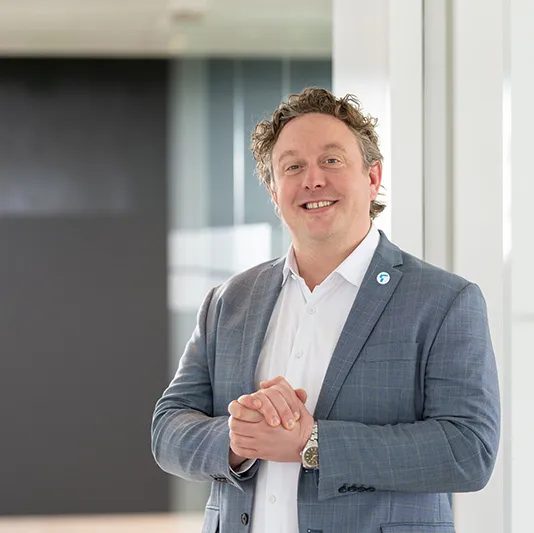
Relevant articles
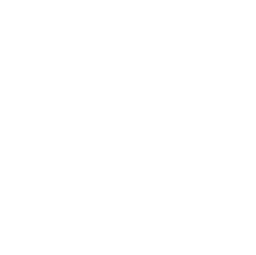
Subscribe to our newsletter
and stay informed!
Newsletter is sent out monthly. No spam. You can unsubscribe at any time.